ものづくりの変革に伴う今後の調達業務
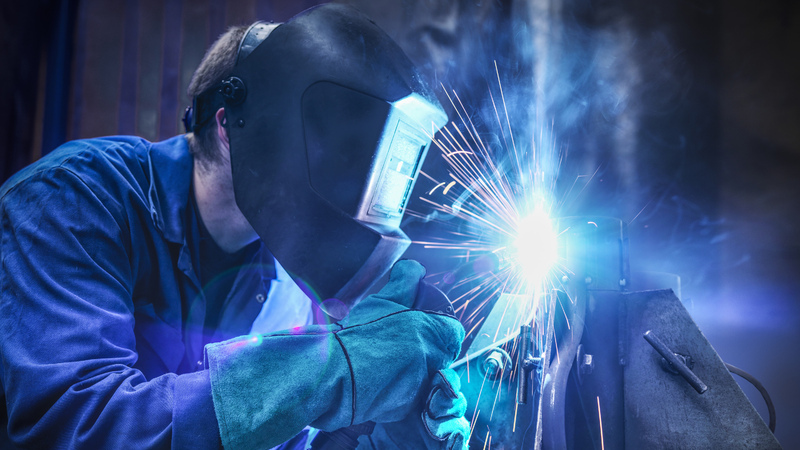
製造業のグローバル化とものづくりの変革が進むなか、各企業のサプライチェーンに注目が集まっている。私たち未来調達研究所株式会社も「The調達2016」という冊子を無料公開し、好評をいただいている。
それまでは単に材料を買い集め、生産すればよかったところ、さまざまな変化があふれている。激動の時代に部材調達活動はどうあるべきで、どこに注目すべきか。大手機械メーカーのマネージャーである蒼井蹴人さんに、これからの企業調達について聞いた(聞き手・坂口孝則)。
――ここ最近の問題意識からお聞かせください。
現在、一番危機感を持っているのは「ヒト」の問題である。1990年代初頭のバブル崩壊以降、弊社に限らず各企業が社員の採用を手控えにより、朝日新聞が名付けた「ロストジェネレーション」なる世代が生まれた。現在の年齢にして大卒は30代前半~40代前半、高卒は30歳~40歳の層となる。対してバブル崩壊以前に採用された社員は人数が多い。そのため弊社の人口ピラミッドは45歳以上が多く、最近採用を拡大した開発部門と製造部門に20代は増えたが、30~40歳が少ないいびつな形となっている。
故に、20代がいない部門では40歳を過ぎても新人のやるような業務をしている者もおり、同じメンバーで仕事が固定化してしまっている。仕事が「ヒト」に付き、その人以外では分からないことが多いため、その人が抜けてしまうと仕事が回らなくなる。
経営層であれば、ヘッドハンティングにより他社から優秀な人材を補充も可能だが、ノウハウを継承していく現場の人材にはそれは当てはまらない。弊社も含め、メーカの工場は首都圏には少ないため、優秀な人材の確保は都市部に較べ難しく、特に調達や生産管理などの間接要員は十分な人材を確保できていない。
――それはやはり生産や調達業務に影響を与えますか。
やはりこれでは従来通りに仕事を継承していく事はできず、早ければ5年後、遅くても10年後には現場力の低下という問題が顕在化してくる。10年後にはバブル崩壊以前に入社した現在50歳以上の人材が全員定年退職する。再雇用のシステムはあるが、役職からは外れ、立場も変わり、給与は下がるため、それ以前と同じモヂベーションで仕事は出来ない。経済的な見通しが付いている人はそのまま退職する可能性も高い。
いずれにしても、現在、仕事を回しているスキルの高い人材の絶対数が減っていく。そうなった時、固定化された業務を回せなくなる。
これはサプライヤにも同様のことが云える。特に機械部品の加工を行う中小サプライヤは後継者問題を抱えているところも多い。サプライヤの従業員の高齢化とともに日本企業の大部分が抱える問題ではないかと考えている。
管理部門としては以上の懸念は承知しているが、かといって固定費である従業員を各部の要望に沿って増やすことは、おいそれとは出来ない。
――現状打破の取り組みを教えてください。
製品の競争力アップのためには、機能の向上、速やかな市場リリース、コストの削減を今後も進めていく必要がある。ただし、日本はこれから少子高齢化により就業人口が減少していく。これらに対応するためにも「ものづくり」の変革を進め、先に挙げた「ヒト」の問題も解決していかなければならない。
そのブレイクスルーとして、「ものづくり」の要素のひとつである「モノ」の「運用」で更なる効率化を狙いたい。ここでいう「運用」とは、ITの活用であり、生産方式であり、自動化であり、開発手法である。
開発手法として、現在、自動車メーカのトレンドとなっているのがモジュラーデザインである。モジュラーデザインとはモジュール化戦略の手法であり、フォルクスワーゲンはモジュールツールキット戦略をMQB(Modularen Querbaukasten)と呼ぶプラットフォームを用いてゴルフなどの主力車種に展開している。
また、日産自動車はCMF(Common Module Family)、トヨタ自動車はTNGA(Toyota New Global Architecture)と呼ばれるモジュール化、共通化戦略を推進してX-TRAILやプリウスなどの製品をリリースしだした。
これら自動車メーカのモジュール化戦略には以下のメリットがあると言われている。
「多様な商品をモジュールの組合せで市場に供給できる」
「共通化によりモジュールの数量が増え、量産効果によりコストが削減できる」
「共通化・標準化により取り扱う部品のアイテム数が減り、間接工数が削減できる」
「グローバル拠点から同じモジュールが調達でき、BCPに対応出来る」
弊社は自動車メーカほどの生産量がない機械メーカだが、モジュール化はこれまでも進めてきた。しかし、新規に開発する製品のモジュールは製品毎のアッセンブリにとどまり、機種間で共通に使用できるようにはなっていなかった。自動車メーカに倣って、新たなモジュール化戦略を進めていくならば、商品企画、商品開発時点から製品群全体のモジュール構成を決め、生産方式、サプライチェーンも考慮したものにしていかなければならない。
――モジュール化はそれだけ効果がありますか。
製品の構成品であるモジュールを共通化・標準化すれば、開発・設計の工数は削減できる。当然、開発したモジュールと製品の検証工数も削減できる。同時にプロジェクトの中心に若手を据えれば、開発部門の20代も鍛えられノウハウが次代に繋がる。
製品は検証が終わったモジュールの組合せで構成されるため、量産が始まってからの図面改訂の件数も減る。改訂に振り回されていた生産管理部門や調達部門の間接工数も削減される。更に取り扱いアイテムが減少して、業務自体がスリムになっていく。
モジュールによる生産を進めるためには、今までの生産管理(発注)システムであるMRP(Materials Requirements Planning:材料所要量計画)から、モジュール生産に合った生産システムへの変革が必須となる。その際、間接部門の業務改善も進め、定型化した業務を、ITを活用して少人数で処理できる体制を整えなくてはならない。加えて、部品在庫の持ち方や倉庫の使い方、発注のやり方、物流のやり方も見直していく。
――具体的な変化としては自動化の推進でしょうか。
共通化によりアイテム数が削減され1アイテムあたりの数量が増えるため、自動化は進めやすくなる。今までは製品の機能の満足に重点が置かれ、ロボットなどを使用する自動化まで考慮した設計は一部でしか実現できていなかった。自動化を進めるためには、ロボット溶接やロボット組立が可能な部品形状とし、工順まで考えた設計を進めていかなければならない。
また、インダストリー4.0をはじめとしたIoT化が現在のトレンドであるが、自動化設備は勿論、物流システムにもIoTを導入していく必要がある。現在、物流は人が関与して部品をハンドリングするためにどうしてもミスが発生し、部品と情報の乖離が生じてしまう。発注から見直して部品に情報を紐づけし、生産システムと連携によって管理の省人化も進める。
このように間接・直接業務のノウハウを定型化して蓄積し、自動化、IT化により省人化が、これから起こる人材の減少に対するひとつの答えである。ただ、今までも自動化、間接業務のIT化を進めてきたが、間接要員は減っていない。逆に、IT化によって間接業務が増えている感さえある。今後の「ものづくり」の変革は真水で「ヒト」を減らしていかなければ意味がない。
――次に調達部門に求められるものを教えてください。
調達部門においても、減った人材の補充はされないと考えるべきだろう。そこで求められるのは、製品に付加価値を付けていく人材であり、仕事の進め方も自ずと変わってくる。
まずは開発購買が必須となる。調達部門が企画・設計段階からの入り込み、最適なコスト=「カネ」を作り込む。如何にして最適なコストとするのか、コストの大部分はここで決まる。
企画段階では最初に、「どこで」「何を」「どれだけ売るか」という販売戦略がベースとなる。これに、設計する製品およびモジュールの機能が「どのようなハードウェア・ソフトウェアで構成されるのか」「キーパーツは何なのか」「内作なのか、外作するのか」「その時の調達先・サプライチェーンはどうするのか」などを関連部署と整合していく。
加えて、「どの国の製造拠点で製造するのか」「現地調達できるのか」「為替リスクを考慮したサプライチェーンをどう構築するのか」なども考慮する。また、共通化によってアイテム数は減るが、1アイテムあたりの数量が増える事による「購買戦略」も必要となる。このようなサプライチェーンの構築や製造技術の選定には、現場に近い調達部門や生産技術部門の知識、経験をベースとした意見が重要となってくる。
例を挙げると、特殊で高額な鋳物部品を、国内と海外で生産する製品で使用するのであれば、まず海外製造拠点への輸送費と為替リスクを検討する。現地調達が必須となった場合、海外製造拠点が現地調達できるかどうかを確認。特殊な製法であるが故、調達できない場合は製法を鋳物から溶接構造に変え、どこでも調達できるように設計しなければならない。その場合、現地サプライヤに溶接させるのか、自社の海外製造拠点で溶接するのか、キャパシティも含めた判断が必要となってくる。
このように新商品企画の段階で、部品単位の製法やどの部品をどこから調達し、誰が組み立てモジュールとするのか、などのサプライチェーンを検討し、図面へ反映させ、手戻りのない開発と市場へのスムースな製品供給を行っていく。
――原価についての意識改革はいかがでしょう。
今までの原価に対する考え方を改め、トータルコストを最小化していく。今までは単純に調達品の価格が安ければよしとし、そこにかかる調達部門や生産管理部門の間接工数を考慮してこなかった。
「ヒト」の工数は「カネ」であるとともに、調達リードタイムでもある。例えば、減価償却が終わった加工機を持つ小規模なサプライヤに価格が安いからと発注したとする。そのサプライヤのデリバリーの管理機能が希薄な場合、物流を含めた社内の手間・工数が増えていたら、本当に安いのかを検証しなければならない。
部品が1000円安くなっても、2000円の費用が毎回かかるようでは、トータルでコストダウンしたとは云えない。社内工数・費用の評価軸は管理会計を駆使するため、管理部門と連携をとって進めなければならないが、調達先の選定、サプライチェーンの構築については、このような考え方も必要になってくる。
更に、後継者問題や従業員の高齢化を抱えるサプライヤへの対応をどうしていくかも重要な課題である。例えば単純な部品のサプライヤであれば、海外調達も含め他社へ転注する手がある。
しかし、オンリーワン企業でキーパーツを調達しているサプライヤについては、事業継続を前提としたM&Aなどを仕掛けていく必要がある。資本提携であったり、子会社化であったり、合弁会社設立であったりと、サプライヤの経営に自社が関わるような施策を進めていく。但し、相手があってのことである。これらの施策がサプライヤに受け入れられなかった場合は、その部品を内製化も必要となるだろう。
――同志である製造業のマネージャーに、何か一言よろしくお願いします。
今後、就業人口が減少し、「ものづくり」の現場も開発手法・生産方式の変革、IT化、自動化などにより効率化・省人化が進んでいく。メーカは少数の人員で「ものづくり」ができる「しくみ」を構築が、これから生き残っていくための条件となる。
これに伴い、調達部員には最適コストを作り込むための企画力、社内工数・費用も最適化できるように調達先を選定するスキル(サプライチェーン構成力)が必用となる。更にはM&Aの提案もしていかなければならない。
そのためには、国内外のサプライヤ情報や技術・市場情報はもちろん、社内の業務フローとそれにかかる費用などを認識しておく必要がある。そのようなスキルは一朝一夕には身に付かないが、調達のコアとなる仕事は少数精鋭の調達部員に、それ以外の定型化された業務は有期社員が担っていく流れは止められないと考えている。
――ありがとうございました。
未来調達研究所株式会社では蒼井さん参加の「The調達2016」を配布しています。ぜひご覧ください。よろしくお願いします。