製造業のまったく新しいコスト削減と、調達・購買部門のあり方
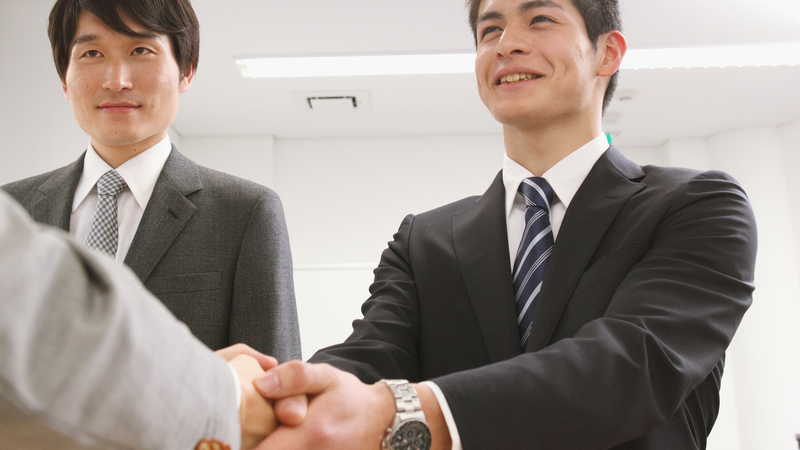
初出:無料冊子「非大量生産時代のコスト削減」の一部を加筆修正して公開
現在、シェアリングエコノミーが流行しています。これは遊休資産の共有ならびに、仲介を指します。たとえば、カーシェアやAirbnbが展開する民泊のように、新たな経済圏と捉える見方は多いでしょう。しかし、これは生産者側からは、将来の生産台数減少を意味します。有名な英国バークレイズ・キャピタルの予想では、2040年までに自動車販売が40%減少するとしています。つまり、シェアリングエコノミーの時代にあっては、モノの生産が減少するのです。多くの業界では、生産量が減り、しかしそのなかでコスト削減をいかに実現するかが検討されています。魔法の杖はありません。そこで、今回は、このような状況のなかで、いかにコスト削減を進めるべきかが企業で議論されています。そこで製造業の新時代におけるコスト削減について、機械メーカーでマネージャーを務める蒼井蹴人さんに聞きました(聞き手:坂口孝則)
――コスト削減を実行する上で重要と考えている三項目についてお話いただけるとのことですが、今日はどうぞ宜しくお願い致します。
微量生産時代のコスト削減について、調達部門はどんな役割を担っていくのか、メーカの製造原価低減への取り組みを軸にこれからの方向性について考えてみたいと思います。
ものづくりを行うメーカは、直接資材費と加工費が製品の原価となります。直接資材費は製造業であれば一般的には50%を超え、組立が主体のセットメーカでは80%を超えるところもあります。メーカの調達部門としては、この製品原価の50%以上を占める直接資材費を削減することが、今までは優先順位一位のミッションでした。
しかし、これから製造原価低減への取り組み方を考えると、現状の調達部門のコスト削減活動だけではなく、俯瞰的にコストを見ていくことが求められているのではないでしょうか。
そこで、コスト削減を実行する上で重要と考えている三項目について、お話していきます。言い古されてはいますが、原価の80%は設計で決まるといわれています。故に原価目標を達成するためには、開発部門、製造部門(生産技術・生産管理)、調達部門で原価を作り込んでいく必要があります。
ここで十分に原価の作り込みが行われていれば、現在、調達部門が行っているような量産してからの資材費の削減はなくなり、社内の組立改善や習熟による工数削減(コスト削減)だけになるはずです。筆者は、コストとは削減するものではなく、作り込むものだと考えています。
しかし、原価の作り込みが不十分であったり、目標原価は変わらないが製品仕様の追加をしたりすることにより、量産してからコスト削減を実施しなくてはならないのが現状です。近年は、微量生産時代を反映し、市場へスピーディーに製品を供給するために開発期間を十分に長く取れないことも、その理由の一つでしょう。
量産後の図面改訂をともなうコスト削減を全て否定するものではありませんが、大きな効果が期待されるとき以外はやるべきではありません。例えば、部品の表面処理をメッキから塗装に変えるだけでも図面改訂が必要です。図面改訂にかかるコスト(設計、発注、在庫処理、生産情報変更など)を計算するとトータルコストは下がっていない場合も多いのです。
――では、このような問題を解決するためには何が必要となるのでしょうか。
私は次の三点であると考えています。
一つめはモジュラーデザインの推進です。スピードが求められる近年の開発において、モジュール化が進めば共通部品や類似部品を活用することで設計期間を短縮できます。それと同時に、コストの作り込みのスピードと精度も確保できます。
二つめは3D-CADの活用によるシミュレーションの強化です。3D-CADはその膨大なデータ量から強力なコンピュータ リソースが必要であったが、近年はソフト技術の進歩により3Dモデルを簡易的に活用し、製品の動作も含めたシミュレーションがスピーディーに行える環境を整備することが可能です。これにより、早い周期で設計のPDCAを回し、原価目標に沿った適切なコストの部品を設計、選定していくことができます。
三つ目は、後述する付加価値を拡大するための施策の設計への反映です。これは、経営戦略に基づいた内外作の判断が必要となり、サプライヤ戦略にも密接に関係するため、経営管理、開発部門、製造部門、調達部門の連携が必要となってきます。
以上の三項目を実践し、開発設計のフロントローディングを推進します。これにより、商品企画からの原価の作り込みスピードと精度を向上させ、できるだけ量産後の資材費削減を行わない状況を作っていかなくてはならないのです。
――付加価値の拡大について、お話いただけますでしょうか。
企業が新たに生み出した価値、付け加えた価値を付加価値といいます。付加価値とは売上高から外部調達費を引いたものであり、利益はここから生み出されます。利益とは付加価値から人件費や減価償却費などの費用を引いたものです。
(付加価値)=(売上高)-(外部調達費)
(利益)=(付加価値)-(人件費・減価償却費などの費用)
従って利益を増やすためには、外部調達費を下げるか、付加価値そのものを増やすか、その両方を行うか、です。
ただし、付加価値とはユーザが決めるものでもあります。ユーザが妥当と考える金額でなければ売上はあがらないのです。販売価格を下げなければ売れないのであれば、ユーザがその商品の付加価値を、メーカが考えているよりも低く評価しているということです。
つまり、魅力的な製品を市場に供給することが付加価値拡大の必要条件でありますが、ここではものづくりのコスト削減に論点を絞り、売上高は変わらないものとして、付加価値を拡大し、利益を増やすという前提で話を進めていきたいと思います。
――では、ものづくりの中で付加価値を拡大するためにはどうすれば良いのでしょうか。
調達品のコスト削減手法を駆使して外部調達費を下げるのは勿論ですが、ここでは自社へ付加価値を取り込んでいく施策について考えてみます。
付加価値を取り込んでいくということは、自社でコントロールできる範囲を増やすということです。簡単にいうと、買い物を減らして自社または自社でコントロールできる製造拠点で内製する部品を増やすということです。
これにより、今まで調達先の利益となっていた費用を自社に吸収でき、ブラックボックスだった費用構造が見えるようになります。費用構造が見えるようになれば、改善によって更にコスト削減できる可能性も広がります。
しかし、自社で内製しておらず外部から調達しているものは、自社にそのリソースが無いからそうしているのであり、これを実行することは簡単ではありません。
――それでは、部品の特性によって必要な施策について、教えていただけますでしょうか。
まず一つめは、自社保有技術で製造できるものです。
自社で設計した部品を、自社またはグループ会社の保有設備や要員を活用または増設、増員し、自社内に取り込みます。
その際、生産量(設備、要員の稼働率)が確保でき、調達先よりもコスト削減できることが必須となります。
そして二つめは、他社と連携して製造するものです。他社に自社で設計した部品の製造を委託する際、生産工程にまで入り込んでコスト構造を見える化し、改善(コスト削減)を推進します。
サプライヤが生産工程や原価構造を開示できるのであれば、それにこしたことはないが、アップル社がFOXCONN(鴻海精密工業)に工作機械などの生産設備を貸与しiPhoneの製造を委託しているように、専門メーカに自社で用意した設備を貸与し、生産工程を全て把握するなどの手法を取ります。
最後、三つめは、自社に無い技術や生産能力を取り込むものです。自社に無い技術や生産能力をM&Aや合弁などによって取り込みます。
最近では鴻海精密工業によるシャープの買収などが挙げられる。鴻海精密工業はシャープのブランド力、40歳以下の技術者、液晶製造技術、が欲しかったと報道されています。
ご説明した三つの施策は全て投資をともなうものであり、製品の生産量、生産拠点、生産期間、販売価格(利益)などが見えないと計画できません。従って、経営戦略、商品戦略に沿って検討していくこととなります。
当然、全ての部品にこれらの施策が当てはまるわけではありません。自社の仕入金額において高い比重を占める部品で、どの部品であれば上記施策が当てはまるのか、採算が取れるのか、その見極めとサプライヤの選定は経営課題となる。その際の情報提供は調達部門が行わなければならないのです。
このような自社への付加価値取り込みによってサプライヤは、一つめ、自社で出来ない付加価値を付けるサプライヤ、二つめに連携してコスト削減を進めるパートナー サプライヤ、そして三つめには、それ以外の通常のサプライヤ、に層別されます。これにより、調達部門にはそれぞれのレイヤー毎にSRM(サプライヤ リレーションシップ マネジメント)が求められます。
――付加価値の取り込みを行うことによって、どうなっていくのでしょうか。
このように、付加価値の取り込みを行うことによって、それまで変動費(資材費)だったものが、固定費(人件費、減価償却費など)となります。変動費が減り、固定費が増えるため、損益分岐点が変わらない、悪くなるような投資はしない、とすると、同じ売上高であれば利益が増えることとなります。ただし、売上が減少して損益分岐点を下回ったときの赤字幅も増えます。
固定費の変動費化によってリスクを減らす戦略もあるが、それだけでは収益力が落ち、競争力の源泉、人材・ノウハウが蓄積されません。リスクを管理しながら、自社の収益力を高めていく戦略が今後必要となってくると考えています。
――固定費の削減について、お話いただけますでしょうか。
付加価値を拡大することによって、一旦固定費は増加します。これを増加したままにせず削減を進め、更に収益力を高めていくことも必要です。
固定費を削減するために、最も効果的なのは人件費削減です。しかし、これは今後、少子高齢化が進み労働力人口が減少していくため、新たに要員削減の施策を設けなくとも自然減に任せることも出来ます。特に年齢別構成率が高いバブル期以前に入社した社員の定年退職などにより10年以内に要員は減少し、固定費は減っていきます。しかし、同時に人に付いていたノウハウも失われていきます。
――どのような対応が必要となってくるのでしょうか。
これに対応するためには、ITを活用した業務の効率化が必須となります。ドイツが進めるインダストリー4.0を始めとするスマートファクトリー化もそれが目的のひとつであるように、生産現場のノウハウを定型化し、コンピュータやロボットなどを活用した生産の自動化を早急に進めていかなければなりません。
それは調達や生産管理などの製造間接についても同様であり、製造間接業務の効率化もスマートファクトリー化の重要な要素です。
そのためには、IT化する前に現状の製造間接業務を定型化し、受注から生産までのフローに潜む無駄を削減、ユーザに製品を納入するまでのリードタイムを縮めると同時に、部品在庫、製品在庫、物流費用、倉庫費用を削減します。その後、これらの業務をコンピュータに置き換え、単なるオペレーションなどの付加価値の低い仕事はアウトソーシングしていきます。
従来もIT化による業務の効率化は実施されてきたが、それによってドラスチックに要員が削減されてこなかった。今後起こるスマートファクトリー化の波と労働力人口の減少によって、これからはリアルに人が減っていきます。
スマートファクトリー化が進み、AI(人工知能)がリーズナブルに活用できるようになれば、製造間接業務における生産管理業務や注文書発行業務に関わる要員は10年後にはいなくなっているのではないでしょうか。
――では、調達部門はどうでしょうか。
付加価値の拡大にともない外部調達費が減るため、一見、調達部門の仕事が減るように感じるがそうではありません。先に述べたSRMなどの業務を中心に、開発調達による原価の作り込み、調達戦略の立案、調達マネジメントなどがコア業務として残っていくでしょう。
――最後に一言お願い致します。
以上に述べたように、直接資材費のコスト削減だけに留まらず、自社が製品に付ける付加価値を拡大し、コスト構造を高収益体質に変革していくことが、今後は求められてきます。
調達部門はカネの流れを見ることができる経理や財務、経営管理といった部署の中では一番現場に近いのです。
このような施策を進める上で、経営戦略や商品企画、開発購買に調達部門が関与していくことによって、より現実的で具体的なコスト削減の施策を進めることが出来ると考えています。
初出:無料冊子「非大量生産時代のコスト削減」の一部を加筆修正して公開
<プロフィール>
蒼井蹴人(あおい・しゅうと)