トヨタが「美顔」ノウハウ活用したエコな新塗装技術を導入
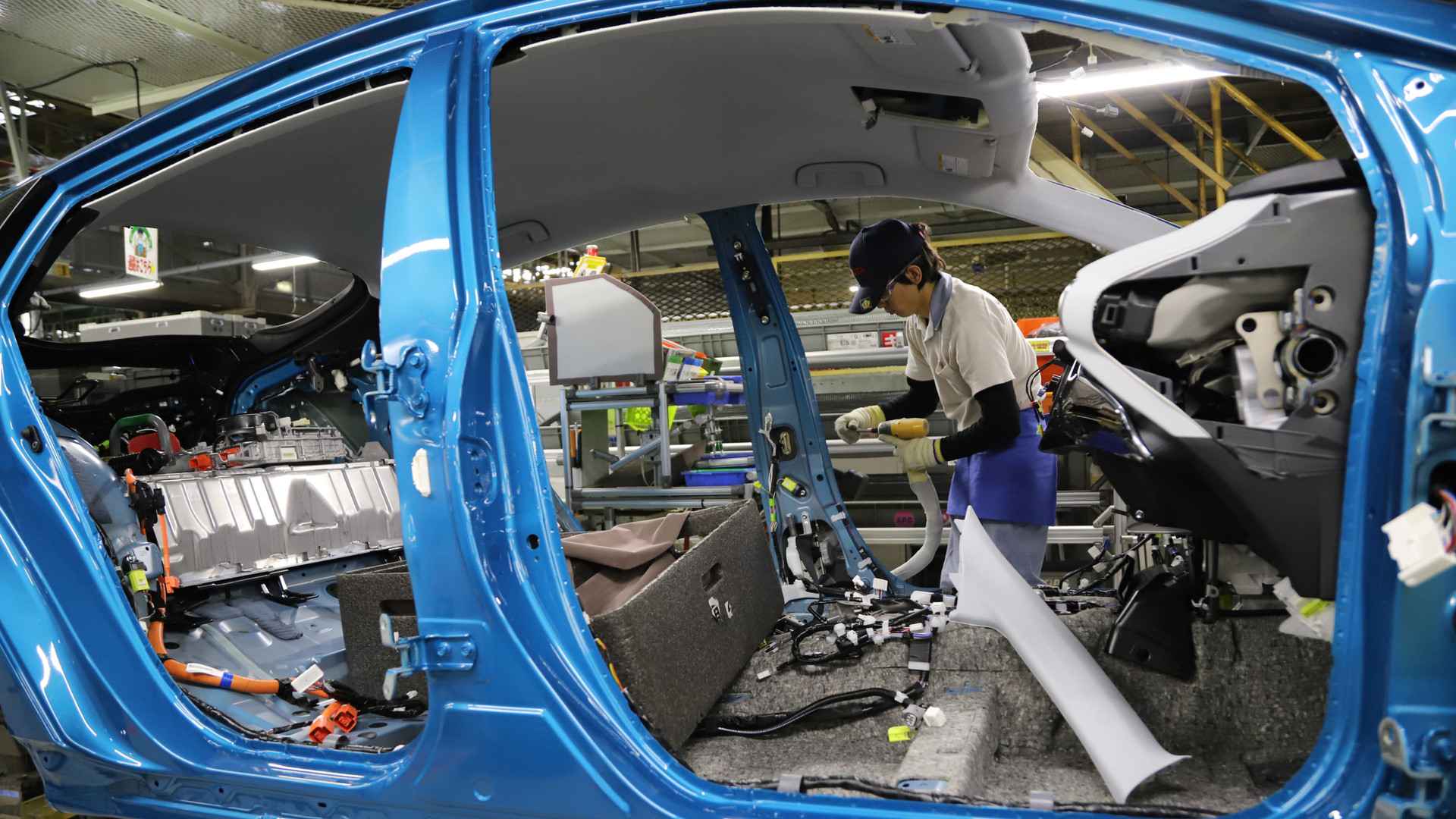
3万世帯分の年間電力使用量削減
トヨタ自動車は、化粧水をムラなく顔に吹き付ける美容機器などに使われている「静電微粒化技術」を進化させた新しい塗装技術を開発した。自動車の生産工程において塗装ラインは、乾燥などで最も電力を使う工程。新技術を使うことによって電力消費が抑えられ、トヨタの試算では従来技術に比べて二酸化炭素の排出量が年間に7%削減できるという。この値は、一般の家庭約3万世帯が年間に使う電力消費量に相当するそうだ。
トヨタは2015年、「トヨタ環境チャレンジ2050」を発表し、その活動の一つに「工場二酸化炭素ゼロチャレンジ」を掲げている。今回の新しい塗装技術の開発もそうした活動の一環だ。
塗料の粒子を「静電微粒化」
新技術についてトヨタではまず高岡工場(愛知県豊田市)と堤工場(同)に導入。さらに海外拠点を含めたトヨタグループ全体で2025年までに導入する。他社向けにも外販する計画だ。
トヨタの新技術の特徴は、静電気の力を利用して塗料を微粒化して車体に吹き付けるもの。これまでの空気の力で塗料を微粒化して吹き付けていた方式を改める。この「静電微粒化技術」は、美容機器では用いられていたが、面積の大きいものには利用できないのが通説となっていた。
しかし、トヨタは「円筒型ヘッド」を開発することで、課題をクリアした。「円筒型ヘッド」には600本の特殊な溝がある。溝の中で塗料を帯電させ、ヘッドを回転させることで生じる遠心力と静電微粒化によって塗料が車体に吸い寄せられる仕組みだ。

塗装効率60~70%→95%に
ヘッドと車体の距離が変化すると電流にばらつきが生じて不安定となり、塗料の粒子の大きさも変化して塗装の均質性が保てなくなる。そうならないために、ヘッドと車体の距離を常に10センチに保ち、電圧を自動制御する技術を開発した。

目標は塗装ブースの大きさ2分の1
新技術の導入によって従来は塗着効率が60~70%だったものが95%程度にまで引き上げられる。塗着効率とは、車体に吹き付ける際に、無駄なる塗料をいかに少なくできるかという値。これまでは使用する塗料の30~40%が空気の力で吹き付けられる際に粒子が車体にぶつかって跳ね返ったり、塗装ブースの中で散乱して床に落ちたりしていた。
新技術では塗料粒子を形成する際に、空気ではなく静電気の力を利用する。帯電した粒子が、「アース」となる車体側に散乱することなく付着するため、使用する塗料が減る。これにより、塗料の使用量は20%減らすことができてコスト削減につながる。目標は塗料使用量の25%削減だという。
また、塗装ラインのブースの床下には水が流れる水槽がある。散乱した塗料をそこに流し、産業廃棄物として処理していた。しかし、新技術では、散乱したり床に落ちたりする塗料が激減するため、水槽の大きさが小さくなるうえ、ブースの清掃作業も簡素化されるため、電力使用量の削減につながるというわけだ。将来的にはブース全体の大きさを従来タイプの2分の1にしていくことが目標だという。
新技術はこれで完成というわけではない。課題も残る。たとえば、車体塗装プロセスには、中塗り層、ベース層、クリア層の3段階がある。現時点では新技術はベース層に対応できない。このベース層は、クルマの商品力を向上させるための重要なプロセスで、外観をキラキラさせたり、はやりのメタリック色にしたりするための塗装をおこなう。
その際のベース塗料には「アルミ顔料(金属分)」が含まれているため、静電微粒化すると、ムラができるなどの課題が解決できていないという。しかし、トヨタは今後その課題も克服して全プロセスで新技術を導入していきたい考えだ。