人材不足を倉庫自動化で解消、ユニクロの有明倉庫をのぞいてみた
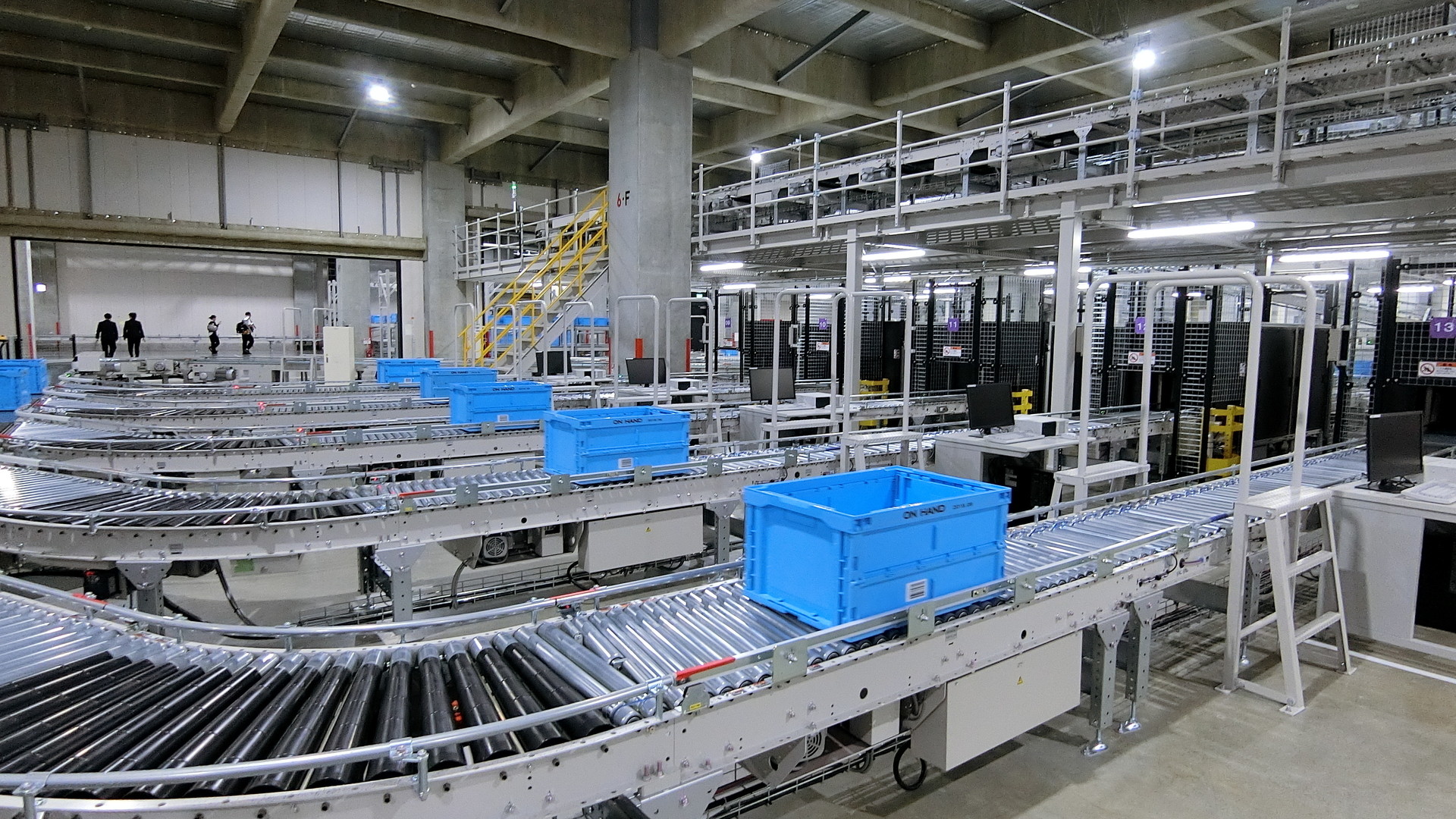
「ユニクロ」(UNIQLO)を手がけるファーストリテイリングは10月9日、サプライチェーン改革を進めるため、物流分野のマテハン(マテリアル・ハンドリング)システムで世界トップクラスのダイフクと戦略的グローバルパートナーシップを提携した。物流費や人員採用難による人件費の高騰などが続く中で、世界中で倉庫の自動化を図り、超省人化・超効率化を実現。情報製造小売業へと進化させ、適時適量適品の調達・在庫コントロールや将来のリアルタイム生産販売に向けて布石を打った形だ。
まずは、ユニクロの構造改革・働き方改革「有明プロジェクト」の拠点である、東京・有明オフィス下に広がるEC向け倉庫(1~3階)の自動化を実施。報道関係者向けにその一部を披露した。
「ザラ」(ZARA)を手がけるインディテックスが世界ナンバーワンの座に就く原動力になったのが、物流・ロジスティクス力だ。「ザラ」のスペイン国内の倉庫内で見られる、ハンガーで吊るされた商品がベルトコンベアで運ばれている姿こそないが、ユニクロの倉庫もおおむねインディテックスと同じ工程や仕組みだ。ただし、ユニクロは後発であるがゆえに、各機械がややコンパクトかつスピード化が進んでいるようだ。
ここでユニクロが採用した工程とともに、自動化による数値の変化をまとめてみた。
海外を中心とした生産地でRFIDタグが装着され、オリコン(折り畳み式コンテナボックス)に詰め替えられた商品は、船便で日本に到着し、トラックに積載され、物流倉庫に送り込まれる。
1)トラックは1階の荷降ろし場に到着。自動入庫荷降ろし機が稼働し、商品の入ったオリコンをベルトコンベアに載せると、3階まで商品が運ばれる。入庫処理能力は従来の20倍だ。
2)3階のRFID自動検品機で検品。黒いボックスを通る際に、正しい商品が入っているかを瞬時に確認。春のテスト稼働から半年間で検品ミスはゼロ。精度は100%だ。これにより検品の作業効率は18倍に飛躍。従来は人間がハンディのバーコード読み取り機で1点1点読み取る必要があり、単純作業のためエラーが出やすく、後工程でのトラブルや在庫の誤差を引き起こす要因になっていた。
3)3階の自動保管倉庫。従来は作業員の身長に合わせた高さで「空気をたくさん保管していた」ものを、天井高いっぱいまで活用することで、保管量は3倍に。こちらは保管キャパシティを重視したストック置き場だ。
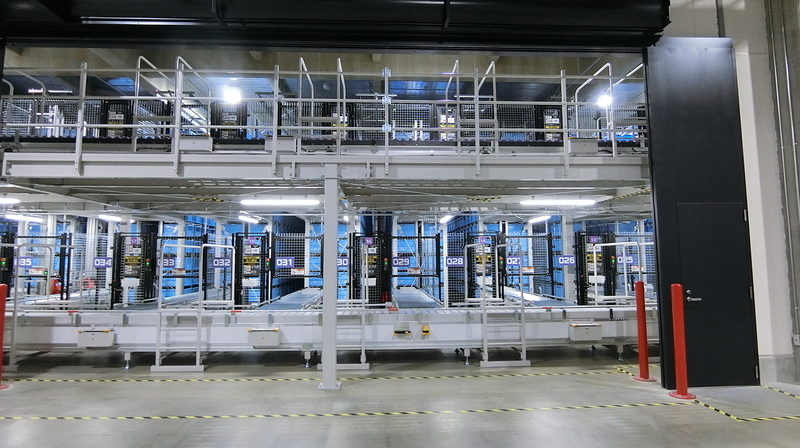
4)一方の2階の自動出庫倉庫は、出荷スピードを重視したストック置き場だ。「ヒートテック」「エアリズム」「ウルトラライトダウン」などヒットアイテムを中心に保管し、オーダーに応じて出荷を行う。2台のクレーンで商品を棚から取り出す。従来は作業員が歩き回りながら人力で集荷を行っていた。
5)同じく2階のクイックピックステーション(通称、QPS)。物流センターの保守・管理担当者などを除くと、人手がかかるのはここだけ。ただし、出荷すべき商品と梱包用段ボール箱が作業員の手元に届くため、歩数はゼロと作業量を軽減。出荷指示書とタッチパネルで確認しながら詰めるだけなので、入社初日のスタッフでも簡単な指導で作業が可能になり、作業効率は20倍に。
6)顧客に送る商品が詰められた段ボール箱は1階の自動封函機に。従来は作業員が注文票と照らし合わせながら確認していたが、こちらもRFIDで瞬時に自動チェック。AIにより、段ボールの内容量によってふたを閉める高さを自動で変更。なるべくコンパクトにされる。トラック内での占有面積が減るため、積載量を増やすことができ、配送効率が数百%向上。コスト削減と二酸化炭素の排出量の削減、資源の省エネなどにもつながる。
7)出荷前の最終工程となる、方面別仕分けソーター。従来は作業員が箱に添付されたラベルの住所を確認して振り分けていたが、新システムでは箱に貼られたバーコードに従って自動仕分けがなされる。配送業者の待ち時間や作業量も大幅に短縮。
ちなみに、従来は人力で行っていた、配送用段ボール箱の組み立てやカラになったコンテナの折り畳みなど、単純かつ労働負荷が大きかった部分も自動化した。
これらにより、現段階で省人化率は90%(人員の9割削減)を達成。入庫生産性は80倍、出庫生産性は19倍、保管効率は3倍と生産性が格段に向上。24時間稼働で、RFID(非接触ICタグ)による自動検品精度は100%。教育コストも80%カットが可能に。これらにより、発注から8~16時間かかっていた出荷時間が、最短15分、最長でも1時間まで大幅に短縮された。
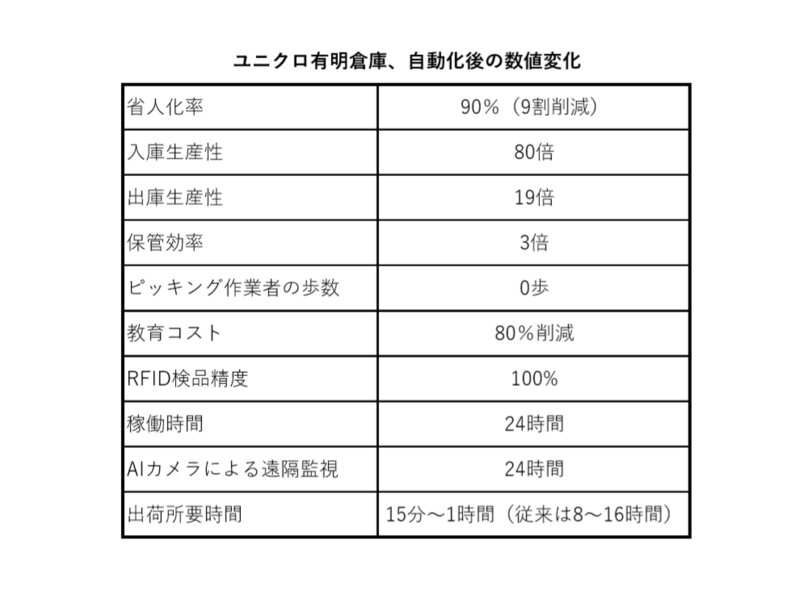
現在、ピッキング作業についても自動化に向けた研究開発を行っており、近い将来の完全自動化・完全無人化を目指しているところ。並行して、全世界の倉庫を自動化し、顧客を中心とした情報製造小売業化を進める方針だ。