製造業の調達担当者へ、新たなコスト削減のススメ
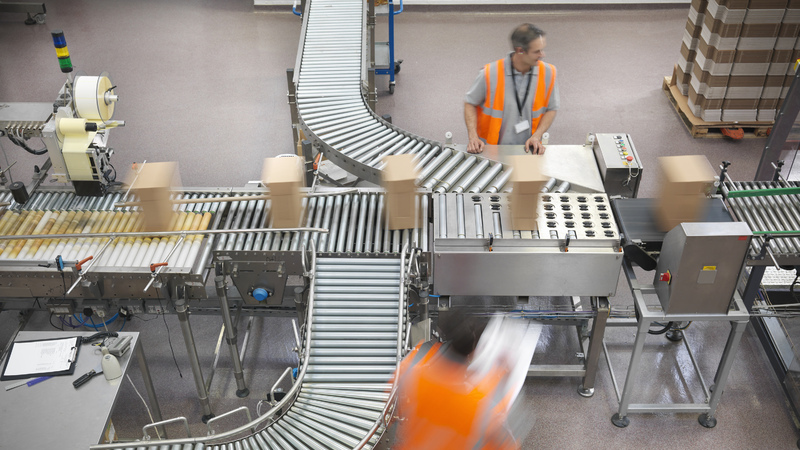
初出:無料冊子「非大量生産時代のコスト削減」の一部を加筆修正して公開
現在、シェアリングエコノミーが流行しています。これは遊休資産の共有ならびに、仲介を指します。たとえば、カーシェアやAirbnbが展開する民泊のように、新たな経済圏と捉える見方は多いでしょう。しかし、これは生産者側からは、将来の生産台数減少を意味します。有名な英国バークレイズ・キャピタルの予想では、2040年までに自動車販売が40%減少するとしています。つまり、シェアリングエコノミーの時代にあっては、モノの生産が減少するのです。多くの業界では、生産量が減り、しかしそのなかでコスト削減をいかに実現するかが検討されています。魔法の杖はありません。そこで、今回は、このような状況のなかで、いかにコスト削減を進めるべきかが企業で議論されています。そこで製造業の新時代におけるコスト削減について、少量生産の企業に勤め、購買マネージャーの倉布惇さんに聞きました(聞き手:坂口孝則)
――さっそくですが、微量個別生産品のコスト削減について、お話しいただけますでしょうか。
微量個別生産品のコスト削減は難しいんですよ。そんなことわかっているからこのインタビュー企画が生まれたと思いますが、いきなり身もふたもない結論で申し訳ございません。
多くのサプライヤーは大ロット生産品をバイヤーに海外サプライヤーへ持っていかれ、それにもかかわらず、バイヤーからはコスト削減を要求され、利益を度外視してコストを下げ、つぶれない程度に細々と会社を続けています。さらには取引額が減ったサプライヤー数社の仕事を別の取引額の減ったサプライヤー1社に集約し、そのサプライヤーの売上が増えることを理由に、またコスト削減を要求する、そんな状態ではないでしょうか。
こんなことがいつまで続くのでしょうか。バイヤーは微量生産でも対応ができ、生産性が高く、コスト競争力のあるサプライヤーを求めているはずなのに、自らでサプライヤーを疲弊させてはいないでしょうか。極論を言えば、こんなやり方は誰だってできます。あなたじゃなくても、他の誰だってできます。しかしながら、読者のみなさんは余人に代えがたい仕事をしたいが為に、この話しを聞いていただけると信じたいんですよね。
――これからのバイヤーについて、どうお考えですか。
これからのバイヤー、微量個別生産のコスト削減に対峙するバイヤーはどうやってサプライヤーと向き合っていくべきでしょうね。言い古された感はあるけれど、自分は生産性が高く、コスト競争力が高いサプライヤーを育成していくべきだと感じています。それができて初めて、微量個別生産品のコスト削減が可能になるのです。
ここでの「生産性」は、一般的に言われている「時間当たりの生産高」だけではなく、サプライヤーの経営資源(材料、資材、資金など)の利用効率を上げることと定義します。
では、生産性の高いサプライヤーとは、どんなサプライヤーでしょう。見積価格が安価なサプライヤーか。それはそれで分かりやすい代用特性であることは間違いありません。でも、本当にそうでしょうか。今までの見積では、そのサプライヤーが投入した経営資源がどれだけ寝ていたのか分かりません。すなわち、その見積価格がどれだけの経営資源をどれだけの期間に投入して算出されたものなのか、「時間軸」での評価ができないのです。
――では何を支えに、何を誇りに走り続けていけばよいでしょうか。
これを評価する方として「面積原価」という考え方があります。ここでそれを簡単に紹介しておきます。
時間軸を含めた「投入経営資源量」は部品・製品の調達、製造、物流のために費やされたすべての原価とその滞留時間の掛け算の総和で表すことができます。これを「面積原価」と定義付けています。
投入経営資源量=面積原価=Σ(原価×滞留時間)
この面積原価を図1に図示する。色が付いている部分が面積原価です。
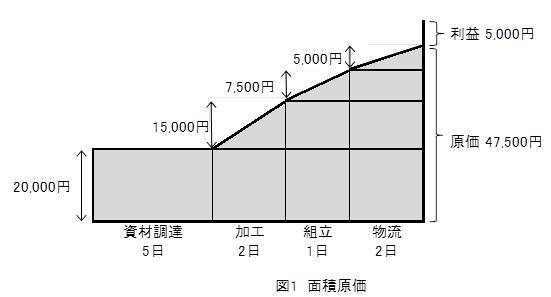
図の面積原価を計算すると
調達部門:20,000円×5日=100,000円・日
加工部門:(20,000円+35,000円)×2日÷2= 55,000円・日
組立部門:(35,000円+42,500円)×1日÷2= 38,750円・日
物流部門:(42,500円+47,500円)×2日÷2= 90,000円・日
面積原価の合計:283,750円・日
図1を見ると、初期に投入された資材の調達コストは、全期間においてサプライチェーンに影響し、そのコストを低減させることが投入経営資源量の削減に効果的です。さらには、原価が積みあがった後の物流では、その滞留期間の短縮が投入経営資源量の削減に効果的なのも理解できるでしょう。このように投入経営資源に時間軸を加えて評価すると、また違った側面からサプライヤーの生産性、競争力に対しての新たなアイデアが出てくるでしょう。バイヤーはサプライヤーと協働し、この「面積原価」を低減させ、真の生産性の高いサプライヤーを育成していくことが微量生産品のコスト削減の第一歩なのです。
――それでは、どうやってこの「面積原価」を低減していけばよいのでしょうか。
おそらく誰もがまずは生産リードタイムを短縮できないかと考えるでしょう。例えば、前述のような事例では、金型を使った生産をやめてみるのはどうでしょう。プレス品は金型をプレス機に設置して材料を投入して、成形する生産方式です。
どうしても金型をプレス機に設置するという「段取り替え」が発生します。この段取り替えは金型を変える際には必ず発生してしまい、この「段取り替え」の間はプレス機が止まっており、なんの付加価値も産みません。かつ、生産リードタイムが増加する一要因です。
「段取り替え」の時間をその部品の生産数数で割ったものが単価にはオンされます。生産する部品数が多ければ多いほど「段取り替え」のコストが薄まるのは分かるでしょう。これが「まとめ発注」「量を背景にした交渉」の根源です。金型を設置して1個しか部品を造らなかったら、「段取り替え」のコストは薄まらずに1個の部品にオンされてしまいます。
これが微量個別生産品のコストアップの要因の一つです。だったら、その「段取り替え」が無い生産方式に変えてしまえばいいだけの話です。換言すれば、金型を使った生産方式は大量生産に適した生産方式と言えるでしょう。
今までプレス機と金型を使って材料から抜き、孔をあけていたものを、別な加工機、例えばターレットパンチプレスやレーザー加工機等を用いて加工することで金型の段取り時間をなくすことができます。これらの加工機は形状等を一度プログラムにデータ入力してしまえば、次回はそれを呼び出すだけで加工ができます。厳密に言えばこのターレットパンチプレスも金型の段取り替えはあるのだが、ここではそれについては目をつぶることにさせて頂きます。
――この他、最近は金属の3Dプリンターなるものがありますが……。
はい、樹脂の3Dプリンターは家庭用の機種も発売されており、結構メジャーな存在になって久しいですけれども、この金属版があります。プリンターと言っても金属の粉末をレーザーによって焼結して成形していく製法で、従来の鍛造や鋳造に比べ型が不要で、材料の無駄も少なく、データを呼び出すだけで成形できる利点があります。
GEは3Dプリンターを用いた部品工場を持ち、航空機のエンジン部品を3Dプリンターで生産しています。弊社でもこの金属3Dプリンターを導入し、メンテ部品などの微量生産に向けて試験等を実施しています。 まだまだ、コストや耐久性等さまざまな課題はあるんですが、近いうちに解決でき、微量生産に寄与できるものと確信しています。
金属加工についてお話ししたが、どんな部品でも、今までの生産方法をまったくの白紙に戻し、新たなその生産ロットに合った生産方法をサプライヤーと一緒に見つけていくことはバイヤーの面白さだと私は考えます。
――今度は少しマクロ的な視点からお話しいただけますでしょうか。
これまではミクロ的な視点から微量個別生産のコスト削減に対峙するバイヤーがどうやってサプライヤーと向き合っていくべきかを述べてきたが、今度は少しマクロ的な視点からお話しします。
読者は担当しているサプライヤーはどのような特徴を持っているでしょう。専用ラインが敷いてあり量産部品の生産に強みのあるサプライヤーなのか、それとも汎用ライン化が進み微量生産にも耐えうるそれなのか。そしてこれらのサプライヤーは今後どのような方向性を向いていくのか、向いてもらうのか、バイヤーは冷静に分析し、見直しをし、サプライヤーに働きかけなければなりません。
サプライヤー戦略を見直すうえで、まずはサプライヤーの製品ポートフォリオを見直しするべきです。図2にサプライヤーの製品ポーフォリオを示します。縦軸はサプライヤーの売上、横軸が利益。右上が厚利多売ゾーンで、以下右回りに厚利少売、薄利少売、薄利多売となります。
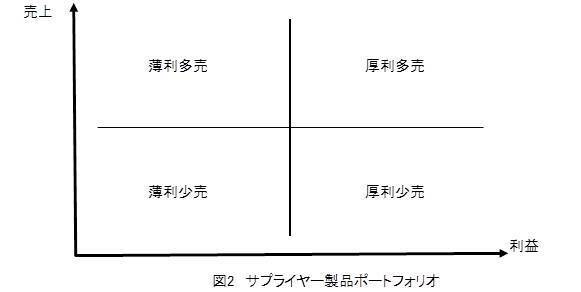
次に、各サプライヤーの売上構成が、どの象限にあるかを描いていきます。図3に例を示します。円の大きさは売上金額、バイヤー企業から見れば購入金額の大きさを模式的に表しています。色が同じなのは同一企業である。通常は一つのサプライヤーで複数の領域のモノがあるはずなので、図3のように一つのサプライヤーで複数の円が描けます。
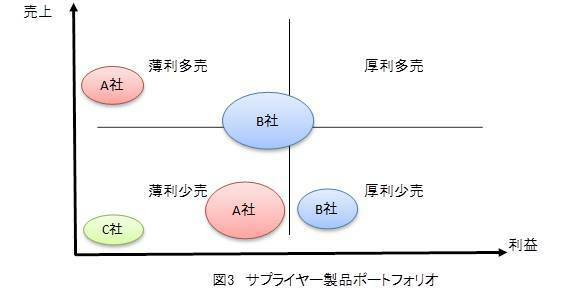
先ほどお話しした通り、海外サプライヤーに大ロット生産品をバイヤーに持っていかれC社のようになっているサプライヤーは数多くいると思われます。バイヤーが能動的に集約するのか、先方から取引停止を申し渡される、はたまた廃業・倒産などの理由でC社のようなサプライヤーは集約の対象となります。
C社よりコストを下げて造れるところがあれば、そこにお願いするのが最適解ですが、そんなことは滅多にありません。見積もりを取ったところA社でもB社でも、C社のコストより上がってしまうなんてことはざらです。それどころか、そんな仕事やりたくないとも言われるでしょう。
それならば、このC社の微量生産品はどこにお願いするべきなのか。例えば、見積もりを取ってB社よりも安価であったA社にお願いします。それも一つの解であるし、A社よりは高いけれど、その他の厚利な部品のコストを下げられるB社にお願いするのも解でしょう。集約を事例としたが、新規品のサプライヤー決定過程においても、このサプライヤーの製品ポートフォリオを考慮し、最適化していくことはサプライヤー戦略上重要なことは自明です。
見積もりを取って一番安価なサプライヤーにお願いするのは簡単であるのですが、簡単であるがゆえに誰でもできます。自らの意志を持ってサプライヤーを戦略的に決定する。そんなところから微量個別生産の第一歩が始まるのではないでしょうか。
――それでは、最後に一言お願いします。
微量個別生産時代のコスト削減がテーマではあるが、サプライヤーマネージメント的なことをお話ししました。昨今、国内のサプライヤーの環境が激変しています。しかし、それに対応できているサプライヤーは少ないです。それはバイヤーにも責任があると自分は思っています。自戒を込めて今後やらなければならないことをお話ししました。サプライヤーと一緒に微量個別生産時代を生き抜く、面白い時代になってきました。
初出:無料冊子「非大量生産時代のコスト削減」の一部を加筆修正して公開
<プロフィール>
倉布惇(くらぬの・じゅん)
現役バイヤー。著書に「調達・購買“戦略決定”入門」(日刊工業新聞社)など。