日産が金型不要のプレス技術を開発 EVはコモディティ化するというのは嘘だ!
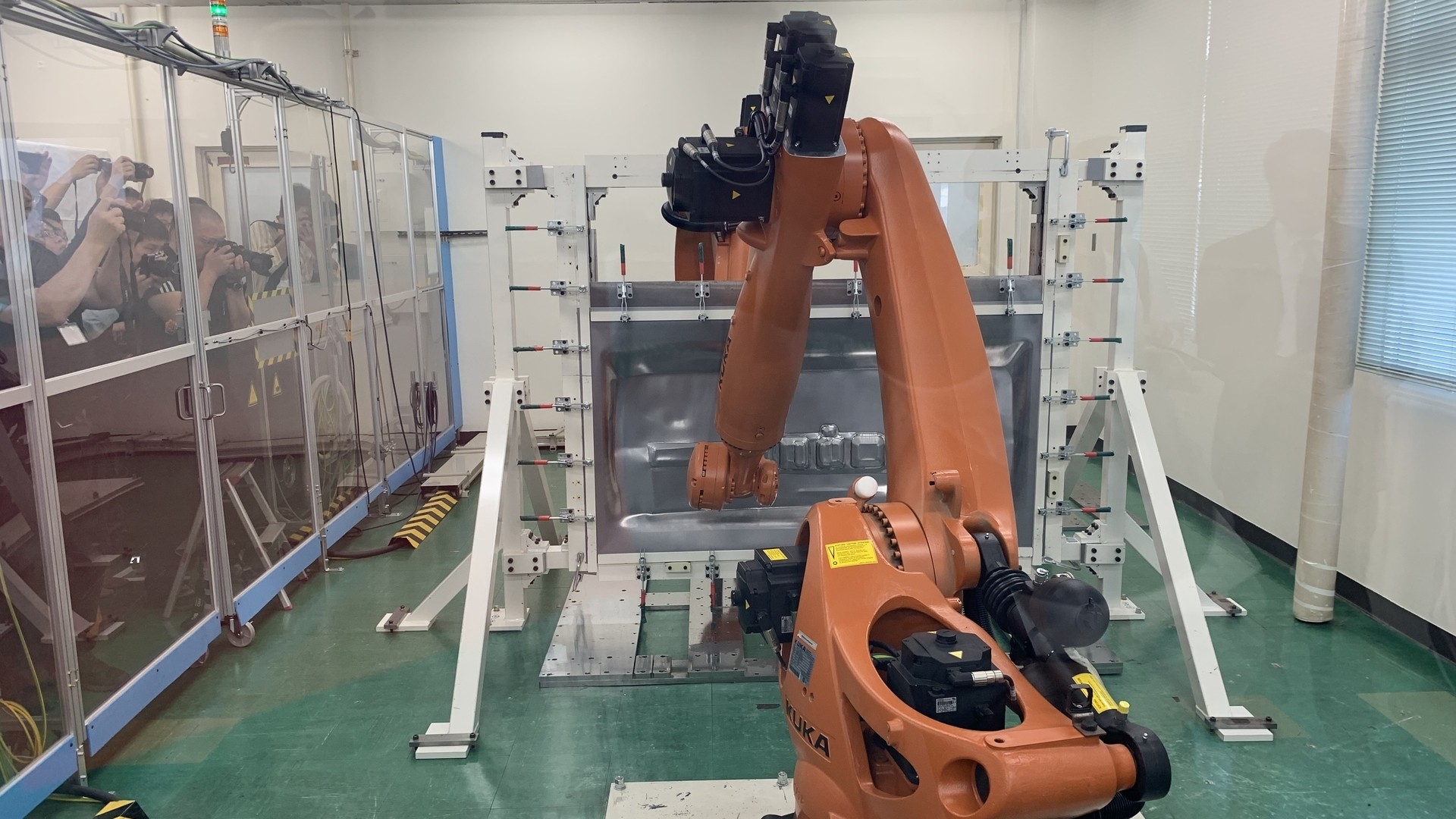
ロボット2台でパネル成型
日産自動車が10月2日、ユニークな新技術を発表した。それは「対向式ダイレス成型」と呼ばれ、金型を用いずにロボットを活用して、鋼板から車体パネルを造る技術だ。2台のロボットが、向かい合う形で表と裏から作業をすることで複雑な形状のものも加工可能になった。超ハイテンなどの材料にもロボットのストローク力を上げれば対応できるという。
現状ではスピードが遅いのが課題。月産100台程度までが上限なので、量産車には向かない。このため、日産は新技術を、たとえば5世代前の「スカイライン」や「GTR」など根強いファンがいる旧型車の修理や、補修部品の生産などで年内中にも実用化する予定。さらに技術革新を重ねて「将来的には月産1000~2000台のクルマには適用できるようにしたい」と日産の坂本秀行副社長は説明した。
デザインに忠実なクルマづくりのために
自動車製造の上流工程では、大型のプレス機械に金型を付けて屋根、ドアなどの車体を成型、それを溶接でつないで塗装ラインに流す。車種ごと、部位ごとに違う金型を用いるが、その開発や保存コストに自動車メーカーは巨費を投じ、償却負担などもかかってくる。量産用の金型を作ってパネルを製作するまでに1年近く掛かるケースもあるが、日産の新技術ではそれが不要なことからパネル完成までに最短で3日程度、最長で1カ月程度で済み、総コストは従来の10分の1くらいにまで落とせる見通しという。金型への投資を増やさずに車種のバリエーションを増やせるメリットもある。要は多品種少量生産には向いているということだ。
金型は固定されているが、柔軟に動くことが可能なロボットが対応するため、加工の自由度が上がって、デザインに忠実なクルマができやすくなる。一般論として、工場や生産技術の制約上から理想とするデザインのクルマが実現できないケースがある。たとえば、ユニークなデザインを考案しても、それをリアルに再現するための設備やノウハウがなかったり、品質が保証できなかったりするケースだ。日産の新技術には、こうした課題に対応する狙いもある。
日産によると、「対向式ダイレス成型」はプロトタイプの小さな部品ですでに適用事例はあるが、リアパネルのような大きな部品に関しては実用化の事例は発表されていないという。
CASEの時代に求められるバーチャルとリアルの融合
新技術のもう一つのポイントが、日産が自社開発したダイヤモンドをコーティングした工具を活用することだ。鋼板の表面を加工する際に摩擦を低減することができ、かつ無潤滑化(ドライ加工)もできるため、「表面品質」の向上と環境負荷の低減にもつながる。
日産はこの技術を開発するのに約5年かけたという。成型後に違う形に変形しない、加工後に材料特性が変化しない、加工表面に粗さがない、といった3つの課題を克服するのが大変だったそうだ。
自動運転やEV(電気自動車)の時代になると、ソフトウエアの比重が高まってクルマの部品点数も減り、かつ構造もシンプルになっていくのでクルマのコモディティ化が進む、すなわち生産に付加価値が残らないといった論調を見かけるが、それは大きな見当違いだと筆者は感じる。
EV化も含めて、自動車産業には、いわゆる「CASE=つながる、自動運転、カーシェア、電動化」の技術革新の波が押し寄せている。さらに言えば、移動の需要をAIが判断してタクシーを呼ばなくても来る時代が到来するなどクルマとビッグデータの融合も加速している。
こうした時代にこそ、顧客に安全で快適でかつ適正な価格で製品・サービスを提供するために、リアルとバーチャルの融合が求められている。すなわちハードとソフトを確実にすり合わせたり、アイデアというバーチャルをモノというリアルに落とし込んだりするノウハウが求められているのではないだろうか。そうでないと、発想はあっても実現に結びつかない「机上の空論」になってしまう。

多様な顧客ニーズに対応する工場力
このため、日産では同時に、EV(電気自動車)や自動運転の時代に必要な生産技術の開発も強化していく方針だ。たとえば、EVの航続距離を延ばすために車体の軽量化が求められ、材料にはアルミや樹脂などが多く使われるようになる。複数の素材を接合するために、従来のスポット溶接やレーザー溶接に加えて、リベットや接着の新技術の開発も強化していく。
さらに自動運転の技術の進化とともに、クルマに装着するセンサー類の数が増加しているが、バンパーの薄肉部にセンサー類を付けてもデザインが崩れず、かつ効率的に装着できる工法の開発も強化する。このほかにも、車体の一部分に追加で色を増やす際に、マスキング対応では手間がかかるために、それを避けるフィルム加飾技術にも力を入れる。
こうした対応は、多様化する顧客ニーズに対応する「マスカスタマイゼーション」の強化でもある。自動車メーカーは、CASE領域の強化のために技術の多様化に投資をし、かつ、世界の顧客の価値観の多様化にも対応しなければならない。その対応として、単に部品を共通化し、派生車種を減らしてコストを削ればいい話ではない。
日本電産の新たなロボット活用術
生産技術は日本の自動車メーカーの「お家芸」だ。工場建設や生産ラインの構築に力を発揮してきたが、これまでは「効率」に重点を置いてきた面がある。今後は生産技術が、市場(顧客)の動向を強く意識し、デザイン・開発とも深く連携していかなければ、新しい技術や発想も「絵に描いた餅」になりかねない。
新時代を見据えて生産技術を強化しているのは日産だけではない。EV時代にモータービジネスの拡大を狙う日本電産も同様だ。子会社の日本電産トーソクは2019年4月から中国の浙江省平湖で、約300億円を投資して最新鋭の工場を稼働させた。生産するのは、新型の「トランスアクスル」。バッテリーを除くEVの主要3部品、モーター、ギア、インバーター(回転数の制御装置)を一体化させたもので、年間70万基の生産を計画している。小型軽量化を進めたことで容積は従来タイプより30%減らし、重量は同程度の出力を持つガソリンエンジンのほぼ半分だ。
モーター製造に求められる総合力
新工場で注目されるのが、「バリ取りロボット」だ。モーターを保護するためにカバーするアルミ製の「ハウジング」にできたバリを取ってくれるロボットだ。「バリ」とは鋳物製品などに発生する金型などの跡だ。ハウジングは複雑な形状をしている。軽量化のために薄さと軽さが求められるが、車軸を受ける部分があるため、強度も求められる部品だ。
手作業でバリ取りをすると、1個処理するのに10分程度かかるが、ロボットだと2分で対応でき、将来的には70秒まで短縮させることを目指す。旧工場では類似製品のバリ取り作業が行われていた。鋳造した製品をいったん籠の中にためて、手作業で作業員がバリ取りをしていた。日本の工場でもこうした手法が続いているそうで、中国の方が一歩先を行っているとのことだ。
このモーターハウジングの製造には、冶金、切削加工、表面処理、流体力学など様々なノウハウが融合している。EV時代にもモノづくりの総合力がなければ、現実に対応できないということだ。